Custom-made
The MOTA Group is specialized in the design and manufacture of customized heat exchange systems. For more than 60 years, MOTA has been supporting its customers in new product developments for mass production (50 to 20,000 units/year). MOTA provides services that meet the most demanding quality management requirements, at very competitive prices.
Tailor-made development is generally suitable for projects intended for mass production over several years (more than 50 per year), and involves joint development with shared investments (time, resources, financial). Heat exchange systems designed in this way are then produced under exclusive contract for our partners.
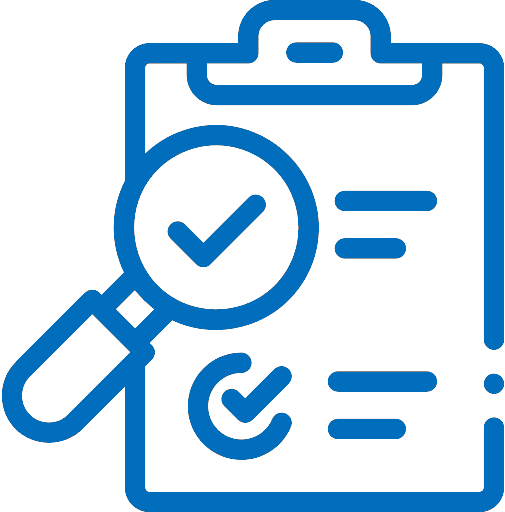
Quality and price
MOTA provides solutions that meet the most demanding quality management requirements at competitive prices. We owe this success to three key aspects of our production management:
- A quality system based on the highest industrial standards.
- A highly streamlined production precess.
- Highly flexible production capacity.
In addition, this production organization makes it possible to compress manufacturing times and meet tight deadlines.
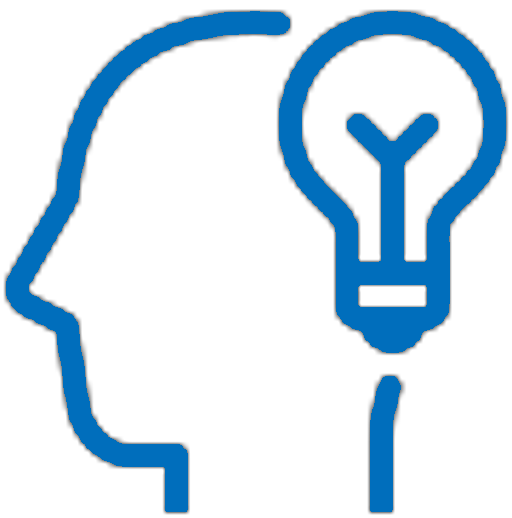
Specialized expertise
Mota has a project team that collabirates with all the precess drivers. The team draws on its experience to guarantee project feasability and provide personalized advices.
This ensures efficient, reliable system design. Our design integrate a nulber of heat exchange-related functions: thermostats, sensors, pressure switches, etc.
Our ability to manage and control our production resources means we can optimize costs. Our flexible productio organization adapts to fluctuations in small and medium-sized production runs.
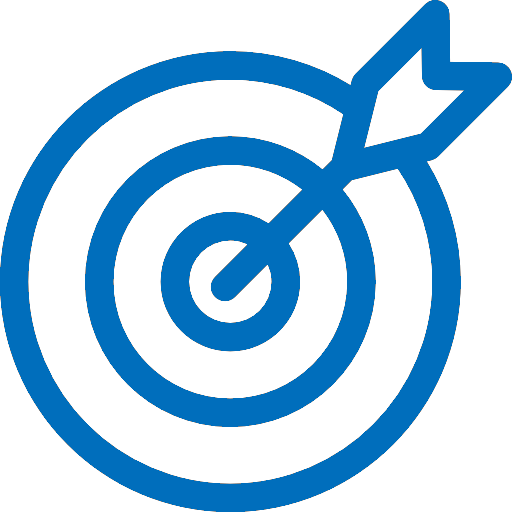
« One shot Good shot » PLAN WELL TO DESIGN WELL
Finite element modeling allows design engineers to predict the behavior of complex assemblies before they are built. It also enables them to optimize part sizing and fluid flow.
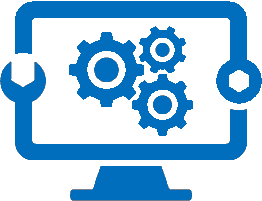
HIGH TECH COMPUTING TOOLS
The design office uses foundry simulation, fluid dynamics (CFD) and finite element analysis (FEA) software to design its new models. These drastically reduce uncertainty, thus avoiding potential risks during product development.
VALUE CHAIN
1. Project study
- Custom development.
- Advice and support from a dedicated project manager.
- Commitment to thermal performance using innovative in-house tools.
- A cost-oriented approach.
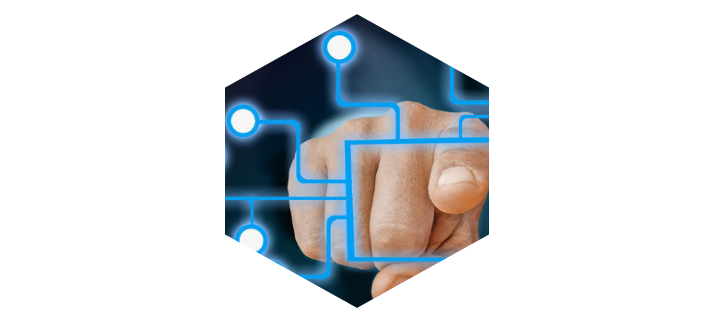
2. DESIGNING A SOLUTION
- Design of complete heat exchange systems.
- Integration of ancillary functions.
- Foundry simulation software, CAD, CAM, FEA and CFD.
- Prototype manufacturing to validate reliability and thermal performance.
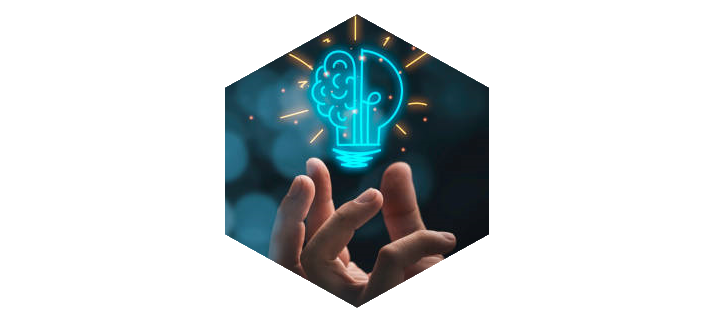
3. MethodS
- Definition of prototyping and production tooling.
- Integration of production processes right from the design stage.
- In-house manufacture of tooling to optimize costs and lead times.
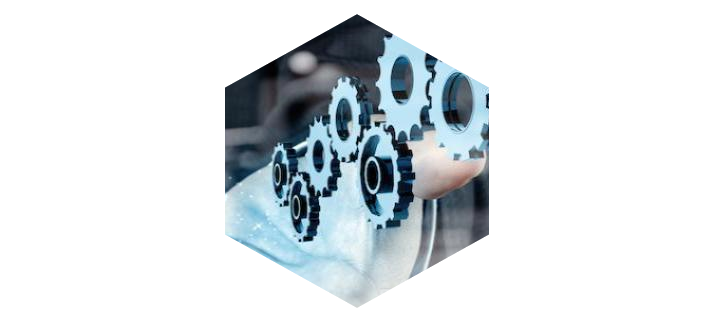
4. SERIAL PRODUCTION
- Flexible production, adapted to small and medium production runs.
- Major investment in production automation.
- Robotization of production processes.
- Production efficiency, quality and traceability ensured by ERP software integration.
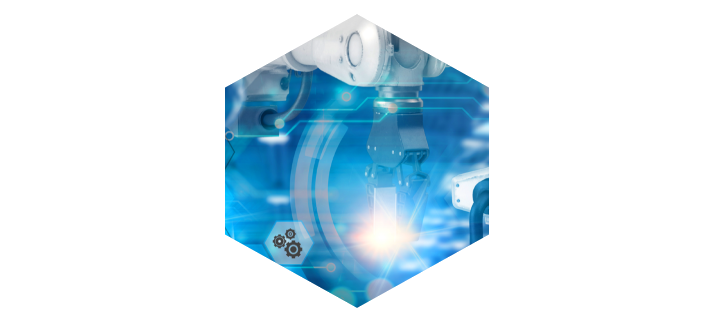
5. QUALITY CONTROL
- Quality system based on the 6 SIGMA method.
- Control and validation at eery stage of production (helium test, pressure test, etc).
- Continuous improvment of quality (ISO9001) and environmental (ISO14001) processes.
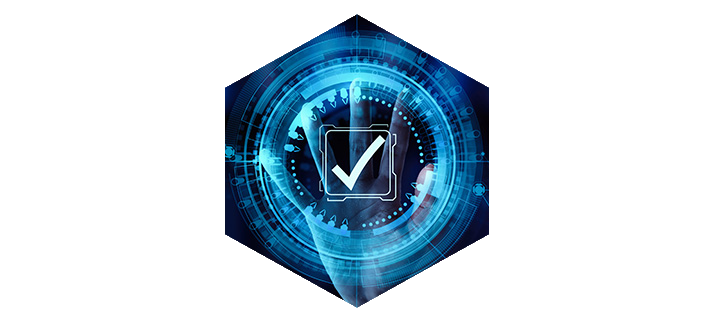
6. LogistIC
- Communication of orders via EDI.
- Close to customers thanks to consignment stocks (USA and Japan).
- "Just in time" delivery commitment.
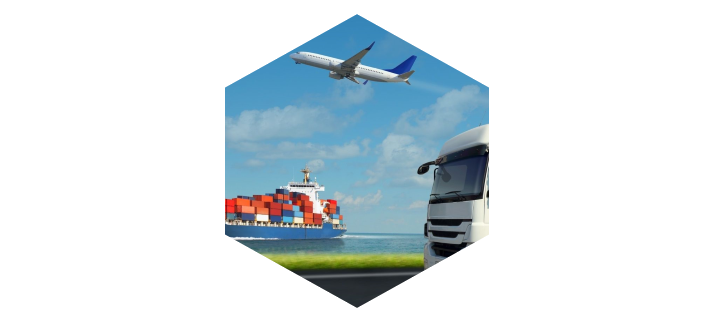
7. MaintenabilitY
- Products designed for easy disassembly and maintenance.
- Quality approach (8D) to respond to after-sales returns.
- Dedicated customer support: our teams are at your disposal.
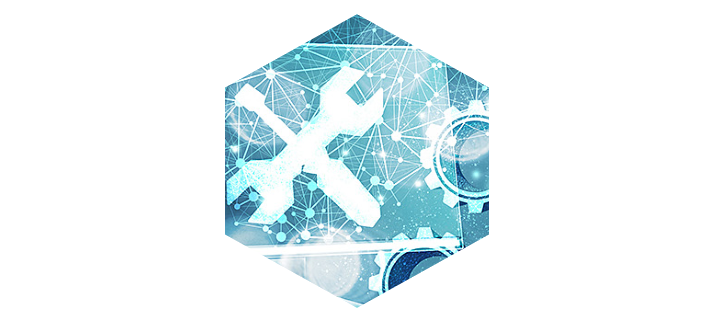
THEY TRUST US
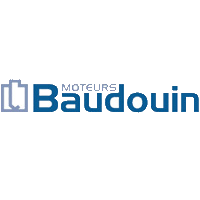
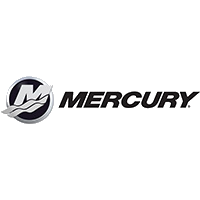
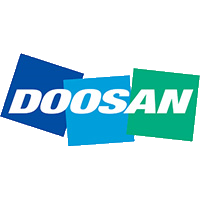
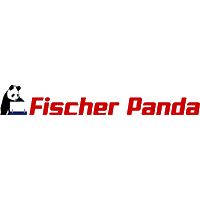
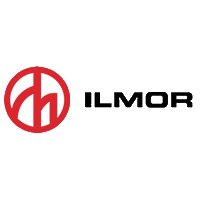
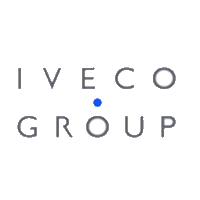
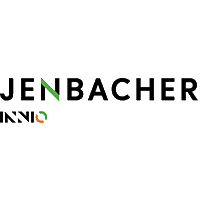
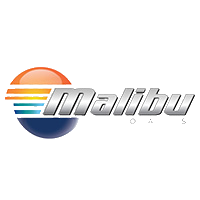
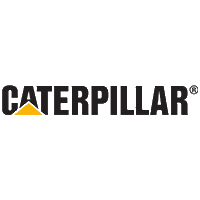
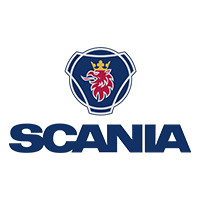
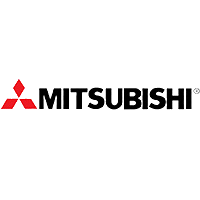
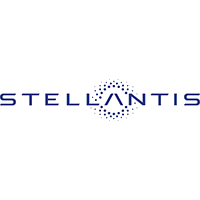
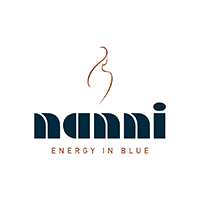
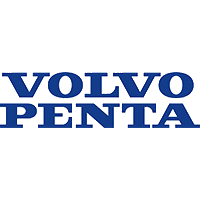
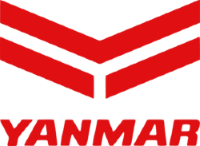
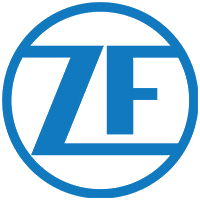
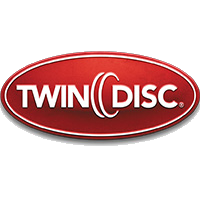
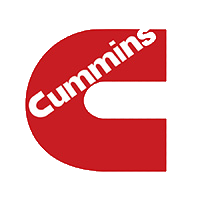
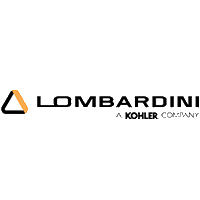